pushing new design frontiers for the future
Albany Engineered Composites (AEC) is at the forefront of advanced composite structures development and innovation. Whether a direct investment or as a collaboration with our technology partners and/or customers, we set the bar solving the most difficult challenges in composite structures and composite part integration. At our core, AEC collaborates with customers for design, co-design, or process design on build-to-print products and assemblies to enable our customers to be most successful.
We are innovating throughout the full footprint of composite and multi-material design solutions to deliver unparalleled performance, rapid industrialization, and affordability. Our long-term and significant investment in unique and proprietary 3D woven composite technologies have delivered unparallel success on the LEAP aircraft engine program and are game changers for next generation aero engines and structures.
Patents & applications pending
Revenue re-invested in R&T
Dedicated to new technology development
3D Woven composites
We are a world leader in the development of technology to aid in the design and fabrication of complex 3D woven composite components for the aerospace industry.
Resin Infusion
We specialize in the development of liquid resin infusion composite processing including resin transfer molding, vacuum assisted resin transfer molding, closed volume molding, and other unique variations.
Robotic Automated Fiber Placement (AFP)
We develop technology around the use of robotic AFP for both thermoplastic and thermoset composites as well as rigid pin installation for through-thickness reinforcements.
Thermoplastic Composites
We are developing the technology around a variety of thermoplastic composite processing methods including pultrusion, injection molding, over-molding, filament winding, and AFP/in-situ consolidation.
Biaxial and Triaxial Braided Composites
AEC has extensive background in design and fabrication of braided structures for composite applications. Our array of braiding machines ranges from 16 carrier to 288 carrier capacity with capability to fabricate biaxial and triaxial sleeving as well as overbraided mandrels for subsequent composite processing. Typical fibers include glass, carbon and ceramic.
High Temperature Composites
We design and develop high temperature composites leveraging our unique textile experience to create differentiating composite solutions. The focused areas of development oxide-oxide, silicon carbide, carbon-carbon, and high-temperature polyimides.
Design and Similation
We have developed a full suite of proprietary design, analysis, manufacturing, and inspection software specifically to support the use of 3D woven composite structures called 3D Composite Studio™.
We have developed and utilizes process simulation tools that allow for as manufactured conditions to be considered in the design and analysis process to reduce development lead time. These simulation tools allows for enhanced prediction of manufacturing conditions such as weaving, preform draping and forming, liquid composite molding analysis, and residual stresses.
Analysis
We utilize traditional composite analysis tools for verification and validation. In conjunction with these tools, we have developed processes and technology around the use of micro computed tomography (µCT) to aid in the development of composite structures as well as their inspection in production.
Gallery
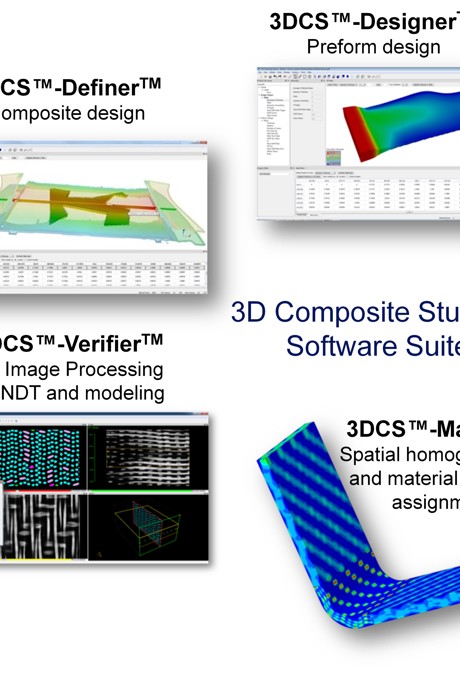
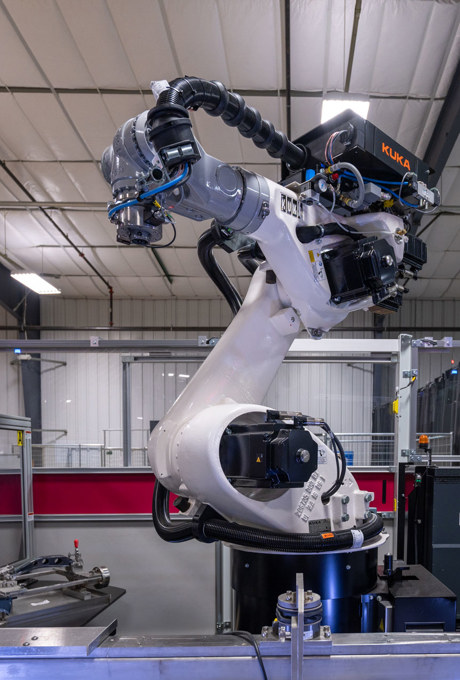
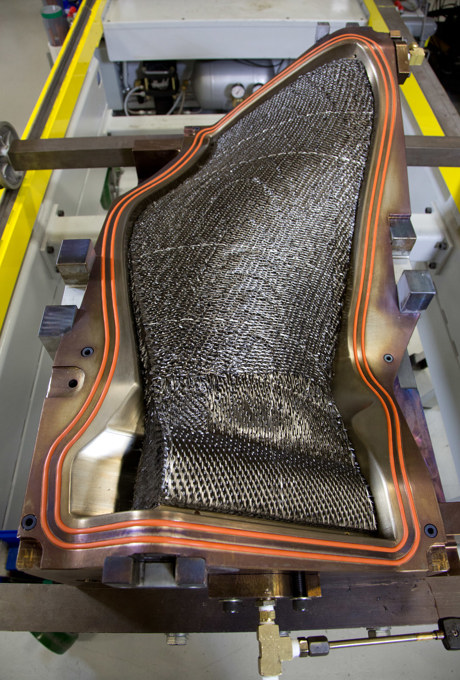
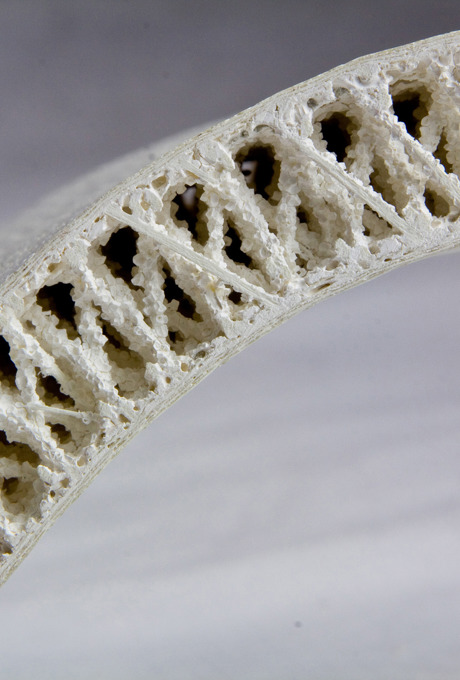
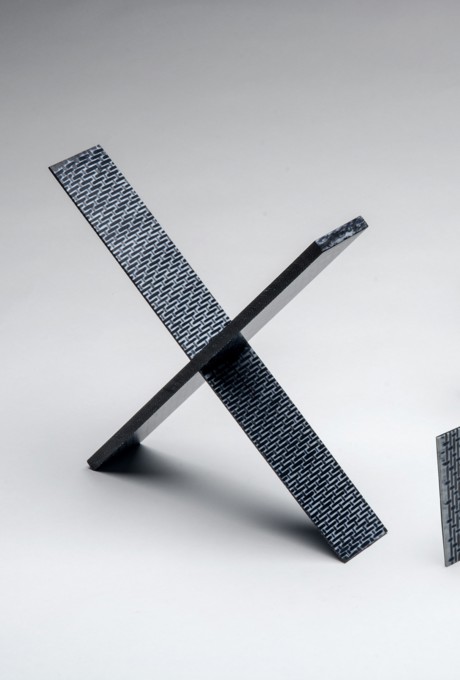
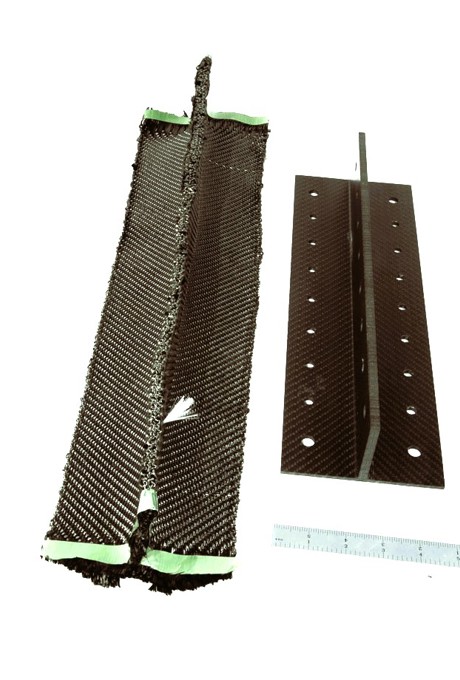
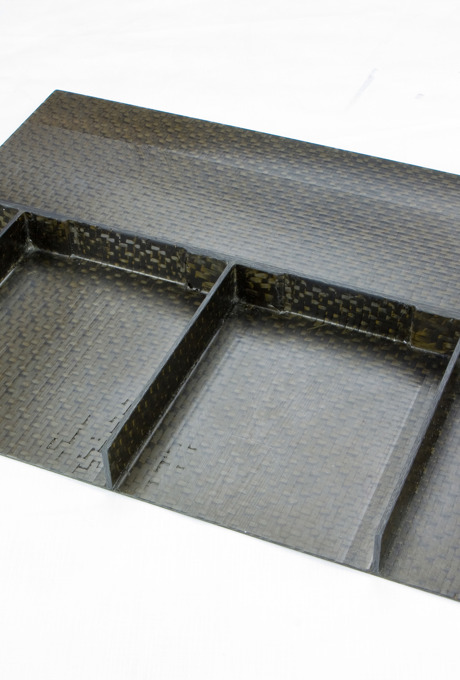
We'd love to hear from you
Let's work together and make great things