An Albany Safran Venture
Engineered Collaboratively for Success: AEC's Impact on LEAP Engine Evolution
Partnered with Safran, Albany Engineered Composites (AEC) has played a pivotal role in co-developing and designing the LEAP engine, a game-changer in the single-aisle aircraft market.
The LEAP engine is the go-to choice for narrowbody aircraft propulsion, setting new standards for efficiency across Airbus, Boeing, and Comac platforms.
The LEAP-1A variant, generating thrust between 24,500 to 33,000 pounds, drives the Airbus A320neo Family's performance alongside Pratt & Whitney's GTF engine. Boeing's 737 MAX exclusively relies on the LEAP-1B (23,000-28,000 pounds), while Comac's C919 is empowered by the LEAP-1C (27,980-30,000 pounds). A defining feature is its 18 carbon fiber composite fan blades rotating within a carbon fiber composite fan case.
As of Safran's December 2022, LEAP engines command an impressive 72% share of the global narrowbody market and a dominant 60% stake within the A320neo Family. The backlog for 10,300 LEAP engines signifies an astounding demand for 185,400 fan blades, marking this engine platform as the world's largest consumer of composite fan blades.
The convergence of high manufacturing volume and uncompromising quality is paramount. Fan blades are a lifeline for aircraft engines, necessitating exceptional reliability to prevent rare blade failures. This dual pursuit of quantity and quality sets a precedent in the aerospace composites.
Since the commencement of LEAP manufacturing operations in 2013, AEC's Rochester facility stands fully industrialized, excelling in high-volume, high-quality composites fabrication. This progress propels AEC into a key leading role within the aerospace market. AEC has since added facilities in Commercy, France and Querétaro, Mexico, also jointly operated with Safran. The plants are AS9100-certified and employ about 675 people.
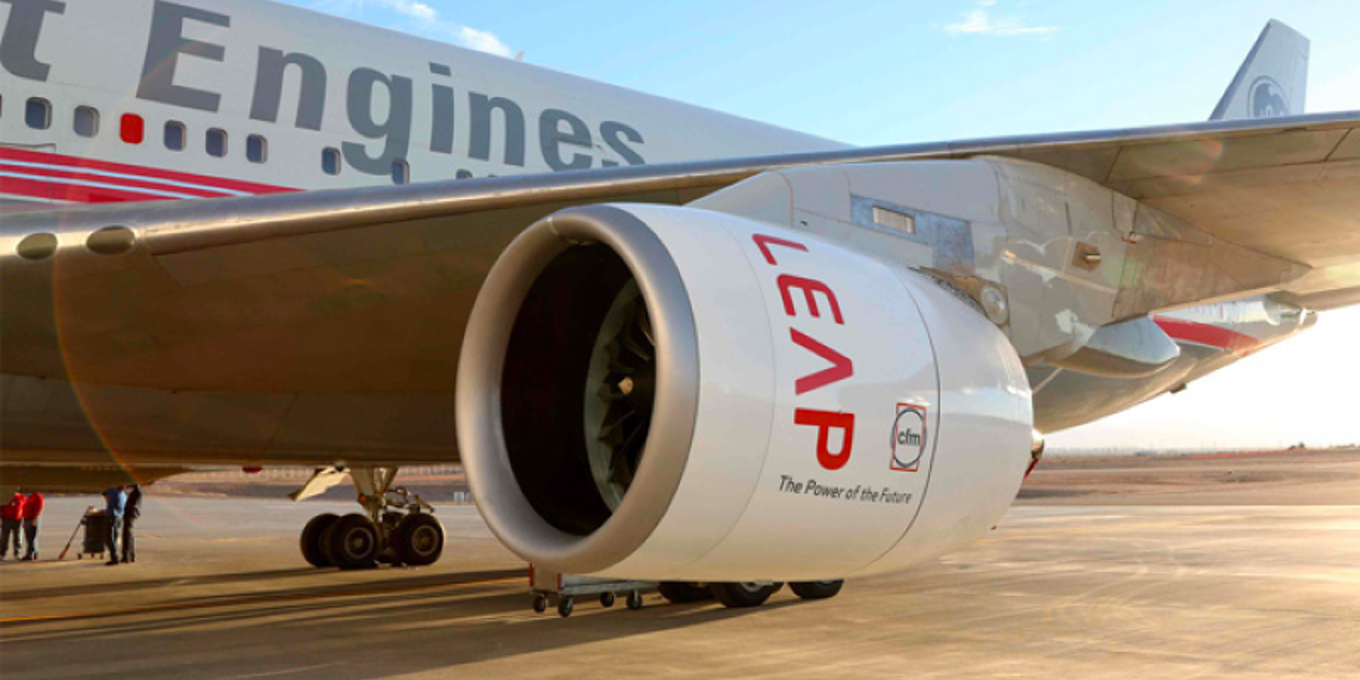
CFM Leap Engine
Unveiling the LEAP Program
The LEAP program is a testament to AEC's expertise and commitment to pushing the boundaries. The LEAP program is core to the Albany Safran Composite (ASC) joint venture. Fan cases, fan blades, and spacers, each an essential part of the propulsion, are manufactured with precision and innovation that reverberate throughout the aerospace industry.
ASC delivers not only quality but also quantity, manufacturing annual quantities of these components that mirror the inverse proportions of their size. One LEAP shipset comprised of a fan case, 18 fan blades, and 18 spacers. This seamless orchestration of parts underscores AEC's dedication to delivering excellence on a grand scale.
Weaving a Future in 3D
At the heart of AEC's success lies its unparalleled expertise in 3D woven composites. With more than 2,000 spooled tows feeding looms, the complexity of weaving at AEC knows no bounds. The results? Through-thickness reinforcement, integrated structures, near-net shape preforming, and the highest standards of automation and minimal waste.
"With 3D weaving, we can offer continuous fiber in the axial direction and continuous fiber in the radial direction. That’s what is unique about our technology, combined with the fact that you have material in that third dimension holding it together. All three of those are coming together to create a really unique preform technology" — Brent Stevenson, VP engineering and technology
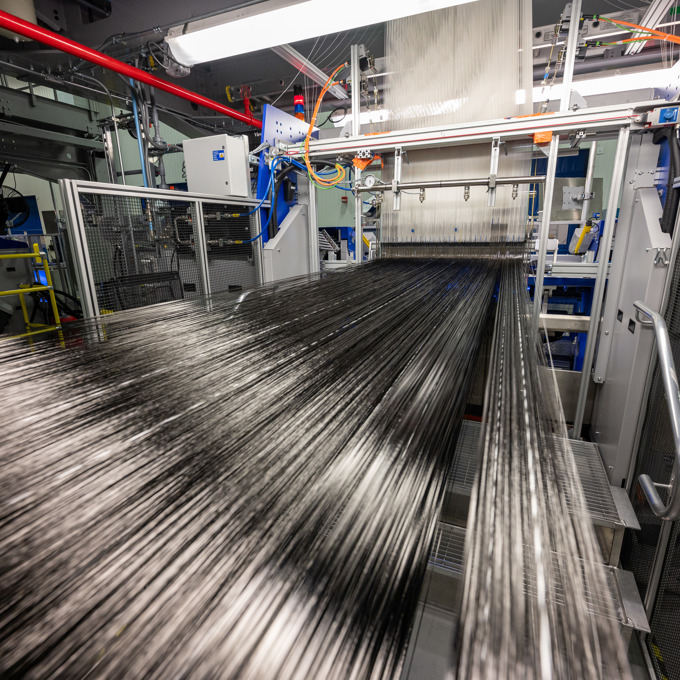
Each loom that performs the weaving is fed by thousands of tows or yarns of carbon fiber
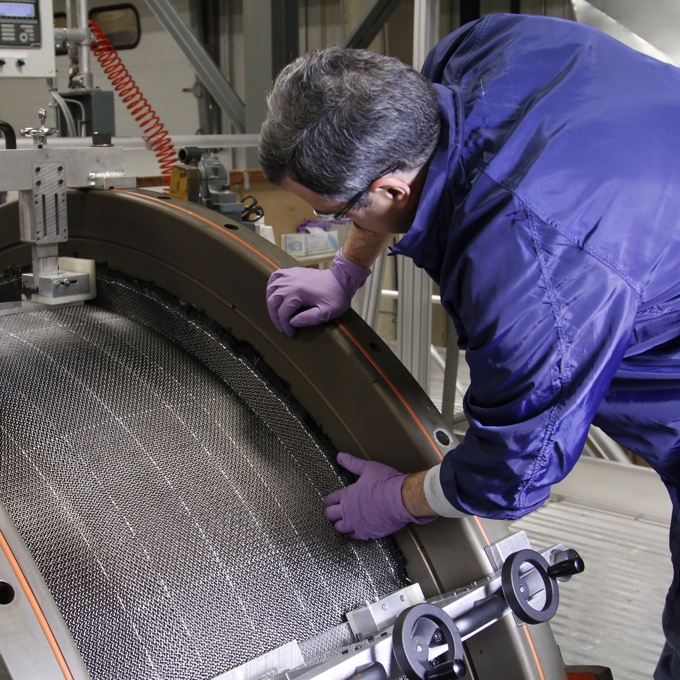
LEAP Engines delivered to Boeing and Airbus
dedicated manufacturing space for LEAP fan case, fan blades and spacers
Operational Excellence: The Drive for Efficiency
Behind every innovation is a focus on operational excellence, an ethos that reverberates through AEC's manufacturing processes. AEC embodies this drive for efficiency. With weaving speeds that have quadrupled since 2013, improved stability, higher machine utilization, and reduced scrap rates, AEC's commitment to operational excellence is palpable. The marriage of advanced technology and operational prowess enables AEC to consistently deliver precision and quality.
AEC's Journey Forward
The ASC joint venture stands as a testament to AEC's commitment to aerospace excellence. With the LEAP program and the GE9X engine, AEC showcases its unparalleled capability to craft complex components that define aviation's future. Through innovation, precision, and operational excellence, the Rochester facility propels AEC into the next era of aerospace manufacturing. As the industry evolves, AEC's dedication remains unwavering, igniting a new age of innovation that redefines the skies and beyond.
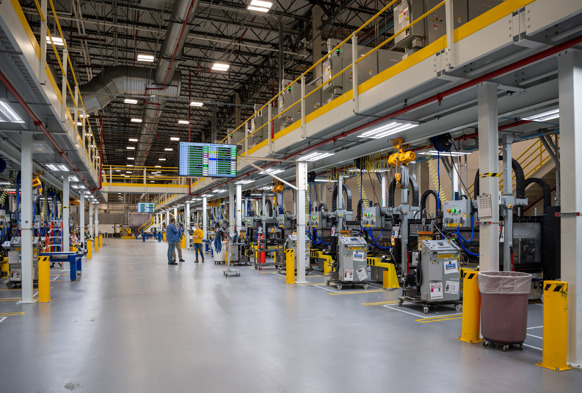
"We have found Safran to be a great partner. They recognize our expertise and let us manage that as we see fit. It’s been a great working relationship over the years." Michael Dill, senior vice president of marketing and business development
We'd love to hear from you
Let's work together and make great things