Improving Fuel Efficiency and Durability
In a joint venture with Safran, AEC have combined our 3D weaving and Resin Transfer Molding (RTM) capabilities to produced lighter, more durable fan cases for the LEAP and GE9X engines.
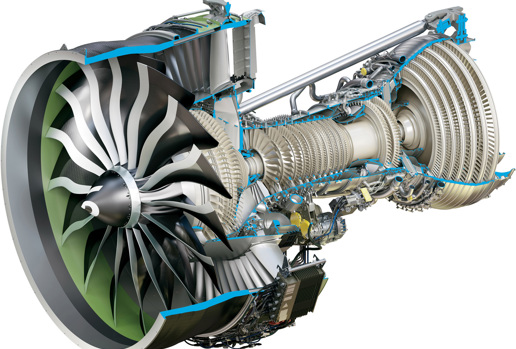
Engine Fan Case
Fan Cases are a critical component of the jet engine that encloses the fan blades. It is designed to contain the damage and prevent it from spreading to the rest of the aircraft in the event of a blade failure, hence its other name - the containment case.
Manufactured by AEC, the Fan Case for both the LEAP engine and the GE9X engine is constructed using advanced materials and sophisticated production methods. The LEAP engine's fan case is about 6 feet in diameter and is made from a composite of carbon fiber and epoxy. The GE9X engine's fan case is approximately 12 feet in diameter and is a structural containment case made of a composite of 3D woven carbon fiber, fiberglass, and epoxy.
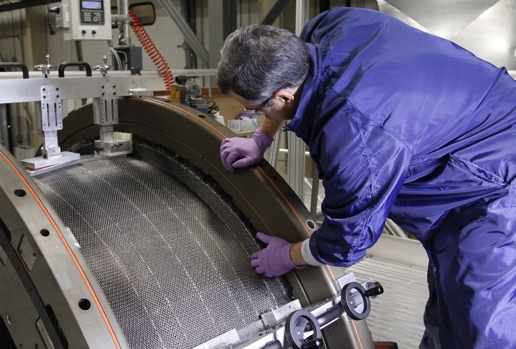
3D Weaving and Resin Transfer Molding
AEC employs cutting-edge 3D weaving and Resin Transfer Molding (RTM) technologies in the manufacturing process. Notably, the LEAP composite fan case combines 3D and contour weaving techniques to create near-final net shape preforms, which are subsequently molded to shape using RTM. The contour weaving technique permits the entire fan case preform, including flanges, to be shaped as a single unit without the need for cutting and darting. The continuous weaving nature of the part helps prevent fiber buckling post-molding.
Technical Capabilities
We'd love to hear from you
Let's work together and make great things