When engineering and tech come together
We’ve applied what we’ve learned from our 128+ years of experience manufacturing Machine Clothing to pioneer 3D weaving technologies to manufacture our composite material. The process involves layering and interweaving fibers in a precise, computer-controlled process to create complex, high-strength parts that allows for the production of lightweight and strong composite parts with high-performance properties. This technology has the ability to produce parts with complex geometries and high-performance properties, such as high strength, stiffness and resistance to impact and fatigue making it well-suited for use in aerospace, defense and industrial applications.
The key to 3D engineered composites is in the material system design – the fiber and matrix materials that will be used as well as the fiber architecture, which describes the directions and relative percentages of reinforcement. By controlling all of these factors, AEC is able to engineer components that meet specific performance goals while simultaneously satisfying component cost, qualification, certification, and eventual production needs.
AEC uses and blends a number of technologies to accomplish 3D or complex structural and performance properties.
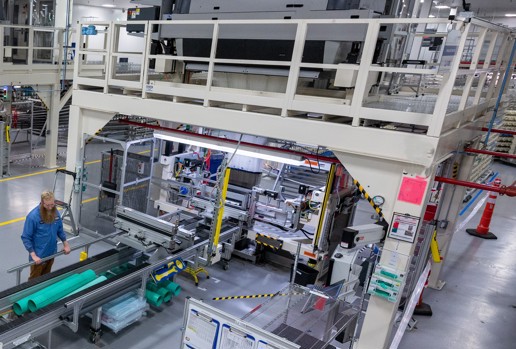
3D Woven composites
Weaving of composite preforms in three dimensions, effectively weaving through thickness reinforcements directly into a component during preform fabrication.
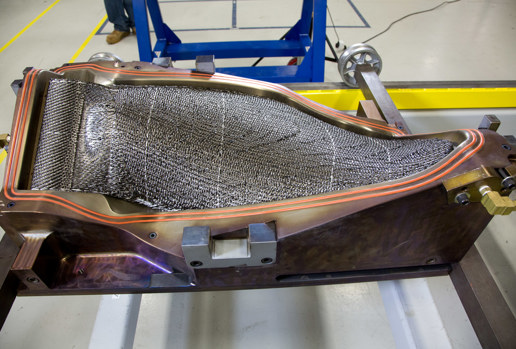
Contour Weaving
Manufacture either single- or multi-layer 3D woven axisymmetric structures with contoured cross sectional profiles, with the intention that the final woven preform shape be similar to the final component shape. This reduces part production costs (because additional preform cutting, darting, or special additional forming is not needed) and improves product structural performance (because the part is continuously woven).
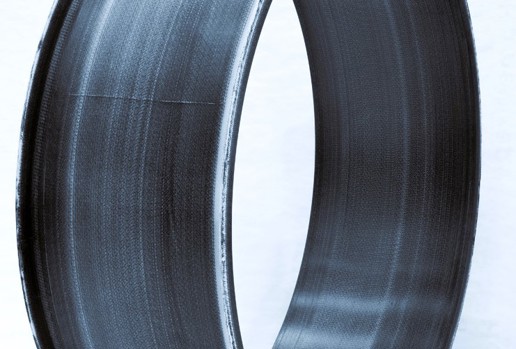
Steered Weaving
We can ‘steer’ fibers when creating single- or multi-layer 3D woven fabrics. The result is a composite structure comprised of reinforcement fibers that turn and follow the natural geometry of the part. This reduces part production costs (because additional cutting, darting, or special additional forming is not needed) and improves product structural performance (because shape is continuously woven).
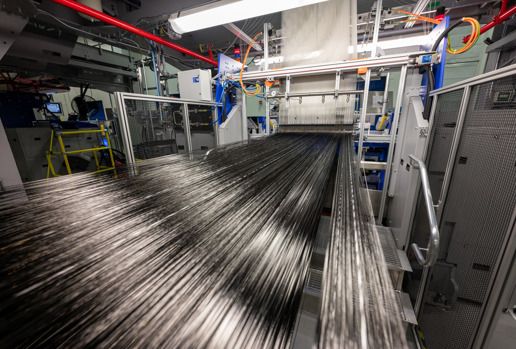
Discrete through thickness reinforcement
We can add additional discrete through-thickness reinforcements to both 2D and 3D woven products in order to improve strength properties throughout a material or specific region of a final component.
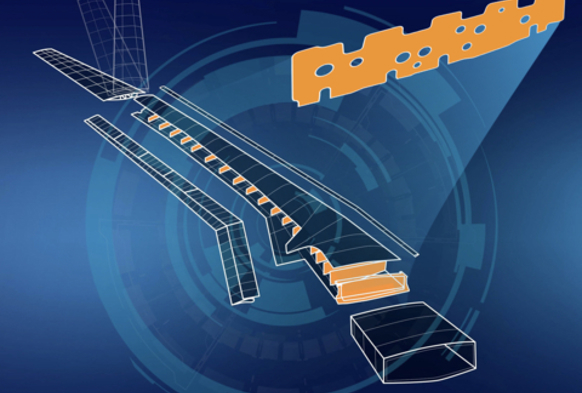
Albany International Is Excited to Deliver Its Advanced 3D Woven Rib to the Airbus Wing of Tomorrow Program
"Advances in digitalization together with composite manufacturing innovations are demonstrating cost effective and higher-rate with reduced waste and energy consumption to produce next generation sustainable and lightweight composites products." Brent Stevenson, AEC’s SVP of Research and Technology
Newsweek: America's Most Responsible Companies
Tons of composites used to date
Where it's made
We'd love to hear from you
Let’s work together and make great things